There are many risks involved when it comes to industrial tank cleaning — both for humans and the environment.
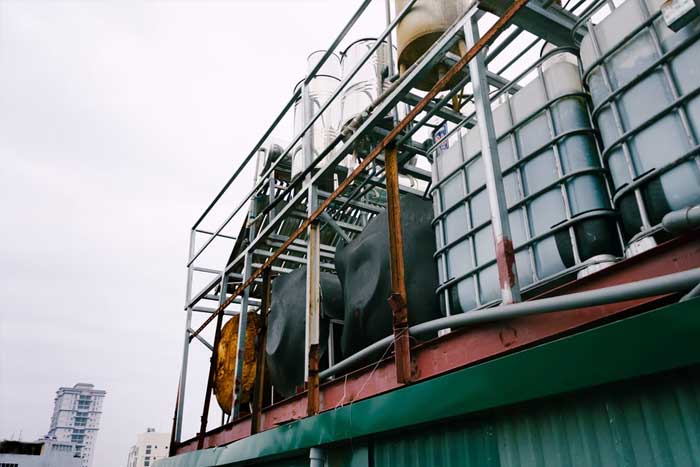
@pwign
Industrial tanks need to be cleaned regularly to ensure the quality of products stays intact and for maintenance reasons. When liquid or other material is stored in industrial tanks, sludge and grime build up within the walls of the tank over time. This sludge buildup can be physical gunk that sinks to the bottom of the tank or a layer of film at the top of the tank. Sludge buildup causes equipment to function improperly or inefficiently and can change the chemical composition of the liquid or material inside the tank.
The traditional method of cleaning industrial tanks includes confined space entry by human crews to manually clean and dispose of sludge buildup. Confined space entry puts workers in a potentially dangerous situation. It exposes them to hazardous chemicals, low oxygen levels, and much more.
Want to know all of the risks involved with tank cleaning? Here they are.
Confined Spaces
During traditional tank cleaning, humans are forced to enter confined spaces.
A confined space is defined as “a space with limited entry and egress and not suitable for human inhabitants.” A confined space has improper ventilation and only one way in and out of the space. Often, they are too small for humans to complete a particular task.
Confined spaces put workers at risk because there is no proper ventilation and airflow. Workers must rely on oxygen tanks and masks to get fresh air. Both oxygen tanks and masks can be faulty or not perform correctly — a simple stumble or bump can unseat equipment, leaving workers to gasp for oxygen. Oxygen deprivation impairs decision-making, which dramatically decreases a worker’s odds of survival. And if a sudden issue occurs in a confined space (like a gas leak), it can be difficult for human workers or crews to exit the tank promptly, putting them at risk.
Confined space entry requires workers to be in optimum physical and mental health, as claustrophobia can easily set in when cleaning tanks. Depending on the size of the industrial tank, cleaning tasks can also take days or even weeks to complete, leaving numerous opportunities for exposure and dangerous situations for the people entering the tanks every day. Because of all these factors, confined space entry is responsible for over a hundred worker deaths each year.
In most cases, modern and innovative ways of tank cleaning, like robotic tank cleaning, can clean tanks 20% quicker — reducing site downtime, increasing production, and protecting workers from the dangers of confined spaces.
Toxic Chemicals
Industrial tanks often hold different acidic, flammable, and toxic chemicals. Inhaling, consuming, or coming into direct contact with these chemicals can leave workers with long-term side effects that can even prove fatal.
A survey conducted by National Tank Truck Carriers (NTTC) showed that thermal burns and chemical contact accounted for 46.5% of all accidents during tank cleaning tasks.
At any facility or plant, tank cleaning procedures should always include proper equipment and protective gear. However, accidents can still happen, so every possible precaution should be in place.
Falling and Tripping Hazards
The second-most common group of workplace injuries that occur during tank cleaning slips, falls, and cuts.
When crews enter industrial tanks, they often use a harness to get dropped into the tank or to climb up and down the outside of the tank. Industrial tanks can be as tall as 180 ft., so a fall from this height can be deadly. While injuries from falls, trips, and slips can be reduced with helmets, sturdy harnesses, and hazmat suits, the only way to completely remove these types of dangers is by adopting robotic tank cleaning.
Fire Outbreaks or Explosions
Fires and explosions are a constant threat during industrial tank cleaning, as many tanks are filled with flammable liquids, vapors, and chemicals.
Three things that need to be present for an explosion to occur are oxygen, a flammable material, and an ignition source — all of which can easily be present during industrial tank cleaning. A single explosion can put not only one or a few workers in danger but entire teams.
It’s critical to conduct thorough tests before tank entry. Safety protocols should always be followed before any tank cleaning is done, but there is always a risk of human error when humans are involved in this process.
Instead, consider tank cleaning methods that do not include close human involvement.
Consider Robotic Tank Cleaning
The best ways to prevent workplace injuries and fatalities during industrial tank cleaning are with proper safety procedures and protocols, protective gear, and the elimination of confined-space entry as much as possible.
Cleaning tanks with robotics that replace human crews can limit these risks.
Ecorobotics, a robotic tank cleaning company, helps reduce the risk factors associated with Industrial tank cleaning. Their tank cleaning robots are remote-controlled from a safe location while the robots remove sludge and clean tanks, leaving workers out of harm’s way. Tank cleaning robots can work faster than human crews, remove the chance of human error, and keep employees safe. Modern tank cleaning methods improve plant output and reduce facility downtime as well.